Refrigerant Gas Monitoring Technology – Photoacoustic Infrared is the most advance technology available for the detection of refrigerant gas. Only Photoacoustic Infrared (PIR) technology can provide a direct measurement of the refrigerant gas concentration that may be present in the mechanical room. To understand the advantages of Photoacoustic Infrared, it is important to first understand how each technology works. Infrared technology is based on the scientific principle that specific gases absorb infrared light at specific wavelengths. This allows us to identify and quantify gas volume by measuring infrared light absorption. Specific gases can be selectively targeted by narrowly filtering the wavelength of the infrared light introduced; thereby avoiding any infrared absorption by other non-targeted gases that may be present in the sample. While all infrared technology utilizes this principle, not all infrared systems measure gas concentration in the same way.
NDIR (Non-Dispersive) or Absorptive IR systems sold by other manufacturers determine gas concentration by comparing an air sample from the machine room to a sample of inert gas (usually nitrogen) stored in the monitor. The room sample and reference gas are individually irradiated with infrared light. The light absorption measured in each gas sample is compared, and the difference between the two determines the concentration. Inaccuracies with this technology can occur when the assumed zero baseline measurement of the reference gas drifts due to changes in room temperature and atmospheric pressure, aging of IR light source, or contamination of the reference cell.
Photoacoustic IR (PIR) eliminates the problems associated with zero drift by eliminating the need to compare results to a reference sample. Photoacoustic IR systems directly measure the changes in pressure that occur when infrared light is absorbed by the refrigerant present in the sample. The greater the pressure, the greater the concentration. Because no comparison to a reference gas is ever used, PIR does away with the possibility of “zero drift.” With Refrigerant Gas Monitoring Technology and Thermal Gas Systems Photoacoustic Infrared instruments, “zero-is-zero.”
CMOS: (ceramic metal oxide semiconductor) CMOS is an older but still useful technology for refrigerant leak detection. CMOS technology is based on the change in conductivity of sensitized metal oxides upon exposure to refrigerant gases. While CMOS systems perform adequately to satisfy the safety requirements of all refrigerants, IR technology is recommended for toxic applications, refrigerant conservation efforts, or in areas where cross contamination by extraneous chemicals is a factor.
Sensitivity of the Refrigerant Gas Monitoring Technology is quantified in ppm, parts per million volume. Both CMOS and Photoacoustic Infrared technologies can deliver adequate sensitivity to meet safety standards that call for an alarm, remote notification, and ventilation at the TLV-TWA (AEL-TWA). The sensitivity of a highly selective IR instrument is 1 ppm; Wideband multi-gas IR is 20 ppm; CMOS instrument sensitivity is 30-40 ppm for HCFC’s, 40-50 ppm for HFC’s, and 60-80 ppm for CFC’s. To put these numbers in perspective, 1 lb. of refrigerant will evaporate to occupy 3-4 cubic feet of volume, thus raising the concentration of a 30,000-40,000-cubic-foot room to 100 ppm.
Selectivity is the ability of the instrument to differentiate between refrigerants. When there is only one refrigerant present in the mechanical room and the likelihood of interfering vapors is remote, selectivity may not be an important issue. This rationale may also apply when there are multiple refrigerants, but they are all of Safety Group A1. When both Group A1, and non-Group A1 refrigerants are present in the same space (link to exposure limit table), or when other halocarbons, or volatile hydrocarbons may also be present, sensitivity can be very important. Physical separation of potential leak sources can also decreases the importance of selectivity, even when two or more refrigerants are present. For the highest level of selectivity, choose a Haloguard IR or II/IR unit.
Refrigerant Gas Monitoring Technology
Choose Thermal Gas System’s Photoacoustic IR for the highest level of monitoring dependability.
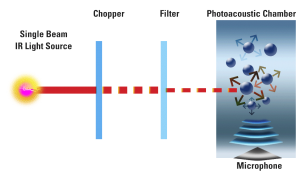
- Because no reference gas comparisons are required, only Photoacoustic Infrared (PIR) technology provides a direct measurement of refrigerant gas concentrations. Other Non-Dispersive IR technologies are subject to “zero” baseline drift when comparing room samplings with a reference gas. PIR eliminates zero drift. With Thermal Gas System PIR instruments, “zero-is-zero.”
- Proven, ultra-precise microphone enables unattended operation for longer periods of time.
- PIR reduces installation and maintenance costs. No need for fresh air sampling line or in-line scrubber required by other IR units.
- Higher operating efficiency. PIR technology eliminates downtime for frequent auto-zero processing common in other technologies.
- Temperature controlled, sealed sample cell in Thermal Gas PIR units eliminates effects of temperature, atmospheric pressure and humidity changes on readings.
- Superior signal-to-noise ratio. Highly selective PIR technology outperforms all others in trace measurment concentrations (1 ppm).